发货:3天内
发送询价
为解决齿轮泵的困油现象,通常在球墨铸铁泵盖上开设对称的卸荷槽,或向低压侧方向开设不对称卸荷槽,吸液侧采用锥形卸荷槽,排液侧为矩形卸荷槽,卸荷槽的深度也比液压工业中所用的齿轮泵要深。
球墨铸铁泵盖放置在刹车泵或离合器泵的储液罐上端。球墨铸铁泵盖上有橡胶密封垫防止刹车液漏出,水分进入。球墨铸铁泵盖可能是塑料或金属制成。形状有圆的,方的或长方的,由螺纹,螺栓或线箍定位。
泵体由吸水室和压水室两大部分组成。在吸水室的进口和压水室的出口分别是水泵进口法兰和出口法兰,用以连接进水管和出水管。在进口法兰和出口法兰上经常设有小孔,分别用以安装真空表和压力表。吸水室一般是一段逐渐收缩的锥形短管或等径直管,其作用是将水流引入叶轮,并向叶轮提供所需要的流态。锥管内常有一隔板,用以避免水流在进入叶轮前产生预旋。压水室的作用是收集叶轮流出的液体,并将液流引向出口。压水室的外形很像蜗牛壳,俗称蜗壳,叶轮就包在蜗壳里。
泵体的顶部设有排气孔(灌水孔),用以抽真空或灌水。在壳体的底部设有一放水孔,平时用方头螺栓塞住,停机后用来放空泵体内积水,防止泵内零件锈蚀和冬季结冰冻坏泵体。泵体由铸铁或铸钢等材料制造,其内表面要求光滑,以减小水力损失。
球墨铸铁泵盖用螺栓和泵体相连,其中部有膛孔,构成填料箱(涵),箱中加塞填料,或采用机械密封等形式高压柱塞泵,以防空气或水从轴和球墨铸铁泵盖之间的缝隙进入或流出。
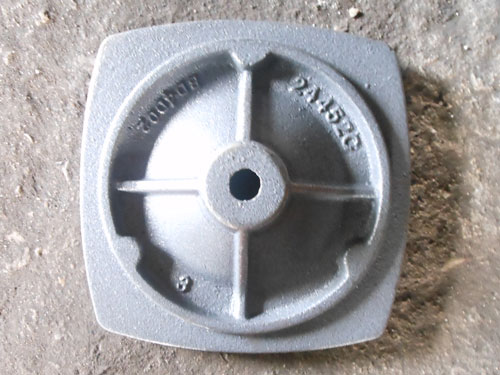
球墨铸铁发动机缸体铸造概况及表面处理工艺
[一]、发动机缸体铸造概况
发动机是汽车的“心脏”,而缸体是发动机中重量重、复杂程度高、生产难度大的一个关键零件。如今,根据发动机结构紧凑、轻量化的设计要求,缸体不仅要有好的内在质量以提高其寿命,还要好的外在质量,包括尺寸精度、形位公差、光洁度以及加工性能等。对于整体式发动机缸体,要求缸筒要有较高的耐磨性,还要耐压、耐腐蚀。康明斯发动机缸体,不仅水泵壳,连机油泵壳、机油散热器壳都与缸体铸为一体。国外为了提高发动机功率,降低油耗,从技术和工艺上采取各种措施提高材质性能以减薄铸件壁厚,减轻铸件乃至整机重量,如今一般中小型发动机缸体的璧厚在3.5~4.5mm之间,壁厚最薄处已不足3mm。要铸造出这样薄壁、强度高、具有复杂内腔的铸件,就对我国的铸造技术提出了更高的要求,不仅要求材质强度高,均匀性好,而且对铸件尺寸精度和表面粗糙度的要求也十分严格。
在发动机缸体铸件的质量、生产技术和工装水平方面,我国与国外存在较大的差距:如尺寸精度,国外一般可达到ISO6~8级,国内较好的汽车、内燃机厂为ISO8~10级。表面粗糙度国外铸件一般为Ra12.5~50μm,国内一般厂为Ra25~100μm,如今,国外很多型号的发动机缸体和车身都采用了铝合金铸造,而我国大部分采用高牌号的灰铸铁铸造,车身架采用的是球墨铸铁铸造。
如今,随着铝质发动机缸体的增多,发动机缸体的铸造方法扩展了许多,如最常用的湿型粘土砂有箱高压造型卧式浇注法;压力铸造、中压铸造、低压铸造都可以用来生产铝合金缸体;金属型铸造可以生产简单的铝缸体;Cosworth法采用冷芯盒砂芯组芯造型,用于生产复杂薄壁铝合金铸件;消失模铸造采用干砂造型,可以生产薄壁、无拔模斜度的复杂铸件;树脂砂型铸造等。
[二]、球墨铸铁表面处理工艺
1、表面淬火和激光热处理
若要在球墨铸铁件表面获得比较高的硬度而心部仍保持一定韧性可采用表面淬火处理的方法。表面淬火处理方法很多,可以是高频感应加热淬火也可以是火焰加热淬火和激光加热淬火等。具体工艺与整体淬火差不多:将球墨铸铁件表面加热到860~900℃,保温一段时间让表面组织全部奥氏体化后再在油或熔盐中冷却实现表明淬火,然后在250~350℃加热保温回火,以使表面组织转换为回火马氏体及残留奥氏体组织,表面组织中的原球状石墨形态不变。处理后的铸件表面具有较高的硬度,心部仍具有一定的韧性。
激光表面热处理除激光加热淬火外,还可在球墨铸铁件表面上实现激光相变硬化、激光冲击硬化等以提高球墨铸铁件的表面硬度。
2、表面化学处理
若要在球墨铸件表面获得非常高的硬度而心部仍保持一定韧性还可采用表面化学处理的方法。球墨铸铁的表面可进行渗氮、渗硼、渗硫以及低温气体碳氮共渗等,现用的比较多的是渗氮和低温气体碳氮共渗。渗氮前一般需要对球墨铸铁件进行退火、正火等预处理,然后用氨作为介质进行二段氮化处理。第一阶段氨分解率20%~35%,保温一段时间后将氨分解率提高到45%~55%,保温后炉冷至200℃出炉空冷,经过处理后球墨铸铁件表面硬度可达900HV,脆性2级。低温气体碳氮共渗同样可以明显提高球墨铸铁件表面的硬度和耐磨性,共渗温度一般为530~570℃,共渗介质为甲酞胺或三乙醇胺50%+乙醇50%。由于球墨铸铁中的碳和硅等元素比较多,可在共渗介质中再添加NH4Cl和TiH2;NH4Cl和TiH2有催渗作用,能加速球墨铸铁的共渗过程。
泊头市艺兴铸造厂(http://www.btyxzz.com)主要产品有搅拌机配件、灰铸铁件、减速机轴、机械加工、端面铣床加工等业务。
球墨铸铁泵盖放置在刹车泵或离合器泵的储液罐上端。球墨铸铁泵盖上有橡胶密封垫防止刹车液漏出,水分进入。球墨铸铁泵盖可能是塑料或金属制成。形状有圆的,方的或长方的,由螺纹,螺栓或线箍定位。
泵体由吸水室和压水室两大部分组成。在吸水室的进口和压水室的出口分别是水泵进口法兰和出口法兰,用以连接进水管和出水管。在进口法兰和出口法兰上经常设有小孔,分别用以安装真空表和压力表。吸水室一般是一段逐渐收缩的锥形短管或等径直管,其作用是将水流引入叶轮,并向叶轮提供所需要的流态。锥管内常有一隔板,用以避免水流在进入叶轮前产生预旋。压水室的作用是收集叶轮流出的液体,并将液流引向出口。压水室的外形很像蜗牛壳,俗称蜗壳,叶轮就包在蜗壳里。
泵体的顶部设有排气孔(灌水孔),用以抽真空或灌水。在壳体的底部设有一放水孔,平时用方头螺栓塞住,停机后用来放空泵体内积水,防止泵内零件锈蚀和冬季结冰冻坏泵体。泵体由铸铁或铸钢等材料制造,其内表面要求光滑,以减小水力损失。
球墨铸铁泵盖用螺栓和泵体相连,其中部有膛孔,构成填料箱(涵),箱中加塞填料,或采用机械密封等形式高压柱塞泵,以防空气或水从轴和球墨铸铁泵盖之间的缝隙进入或流出。
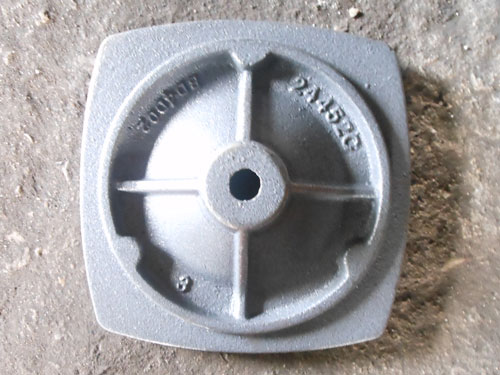
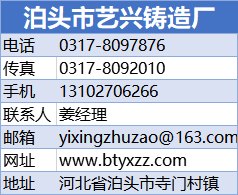
[一]、发动机缸体铸造概况
发动机是汽车的“心脏”,而缸体是发动机中重量重、复杂程度高、生产难度大的一个关键零件。如今,根据发动机结构紧凑、轻量化的设计要求,缸体不仅要有好的内在质量以提高其寿命,还要好的外在质量,包括尺寸精度、形位公差、光洁度以及加工性能等。对于整体式发动机缸体,要求缸筒要有较高的耐磨性,还要耐压、耐腐蚀。康明斯发动机缸体,不仅水泵壳,连机油泵壳、机油散热器壳都与缸体铸为一体。国外为了提高发动机功率,降低油耗,从技术和工艺上采取各种措施提高材质性能以减薄铸件壁厚,减轻铸件乃至整机重量,如今一般中小型发动机缸体的璧厚在3.5~4.5mm之间,壁厚最薄处已不足3mm。要铸造出这样薄壁、强度高、具有复杂内腔的铸件,就对我国的铸造技术提出了更高的要求,不仅要求材质强度高,均匀性好,而且对铸件尺寸精度和表面粗糙度的要求也十分严格。
在发动机缸体铸件的质量、生产技术和工装水平方面,我国与国外存在较大的差距:如尺寸精度,国外一般可达到ISO6~8级,国内较好的汽车、内燃机厂为ISO8~10级。表面粗糙度国外铸件一般为Ra12.5~50μm,国内一般厂为Ra25~100μm,如今,国外很多型号的发动机缸体和车身都采用了铝合金铸造,而我国大部分采用高牌号的灰铸铁铸造,车身架采用的是球墨铸铁铸造。
如今,随着铝质发动机缸体的增多,发动机缸体的铸造方法扩展了许多,如最常用的湿型粘土砂有箱高压造型卧式浇注法;压力铸造、中压铸造、低压铸造都可以用来生产铝合金缸体;金属型铸造可以生产简单的铝缸体;Cosworth法采用冷芯盒砂芯组芯造型,用于生产复杂薄壁铝合金铸件;消失模铸造采用干砂造型,可以生产薄壁、无拔模斜度的复杂铸件;树脂砂型铸造等。
[二]、球墨铸铁表面处理工艺
1、表面淬火和激光热处理
若要在球墨铸铁件表面获得比较高的硬度而心部仍保持一定韧性可采用表面淬火处理的方法。表面淬火处理方法很多,可以是高频感应加热淬火也可以是火焰加热淬火和激光加热淬火等。具体工艺与整体淬火差不多:将球墨铸铁件表面加热到860~900℃,保温一段时间让表面组织全部奥氏体化后再在油或熔盐中冷却实现表明淬火,然后在250~350℃加热保温回火,以使表面组织转换为回火马氏体及残留奥氏体组织,表面组织中的原球状石墨形态不变。处理后的铸件表面具有较高的硬度,心部仍具有一定的韧性。
激光表面热处理除激光加热淬火外,还可在球墨铸铁件表面上实现激光相变硬化、激光冲击硬化等以提高球墨铸铁件的表面硬度。
2、表面化学处理
若要在球墨铸件表面获得非常高的硬度而心部仍保持一定韧性还可采用表面化学处理的方法。球墨铸铁的表面可进行渗氮、渗硼、渗硫以及低温气体碳氮共渗等,现用的比较多的是渗氮和低温气体碳氮共渗。渗氮前一般需要对球墨铸铁件进行退火、正火等预处理,然后用氨作为介质进行二段氮化处理。第一阶段氨分解率20%~35%,保温一段时间后将氨分解率提高到45%~55%,保温后炉冷至200℃出炉空冷,经过处理后球墨铸铁件表面硬度可达900HV,脆性2级。低温气体碳氮共渗同样可以明显提高球墨铸铁件表面的硬度和耐磨性,共渗温度一般为530~570℃,共渗介质为甲酞胺或三乙醇胺50%+乙醇50%。由于球墨铸铁中的碳和硅等元素比较多,可在共渗介质中再添加NH4Cl和TiH2;NH4Cl和TiH2有催渗作用,能加速球墨铸铁的共渗过程。
泊头市艺兴铸造厂(http://www.btyxzz.com)主要产品有搅拌机配件、灰铸铁件、减速机轴、机械加工、端面铣床加工等业务。